The electronic (or alternatively pneumatic) power valve has the task of making the engine, which is designed for high revolution speeds by the resonance exhaust and the pre-exhaust (difference in height of the exhaust channel to the intake channels in degrees of the crankshaft), driveable even at low speeds. This is done by changing the control time of the exhaust channel by using a valve called the power valve or exhaust valve.
With the high pre-exhaust, the pressure waves generated in the resonance exhaust are used to first support the fresh gas flush process with lower pressures and then, with a pressure wave reflected at the counter-cone, the fresh gas, which is in the outlet at the end of the scavenging process, is pushed back into the combustion chamber shortly before the outlet is closed.
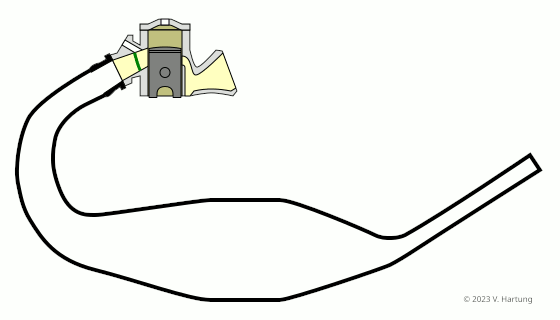
This effect only works in a certain rpm range, which can be influenced by the design of the resonance exhaust. If the engine rpm is too low, the reflected pressure wave (red) will arrive at the combustion chamber way too early.
If the engine is run as it was built (high pre-exhaust) without using a power valve, the effect of the resonance exhaust will start at this specific speed, at lower speeds the engine simply does not have any torque. The waves are reflected way too early and the outlet port is open too long.
For low speeds, the control time of the exhaust port must therefore be changed so the effective compression is higher and compression is started earlier. Such a smaller exhaust duct would then again be too small for high revolution speeds.
The task of the power valve is to switch between these two engine characteristics (with resonance exhaust and high fore exhaust and with closed slide valve) at the right time – or rather at the right speed.
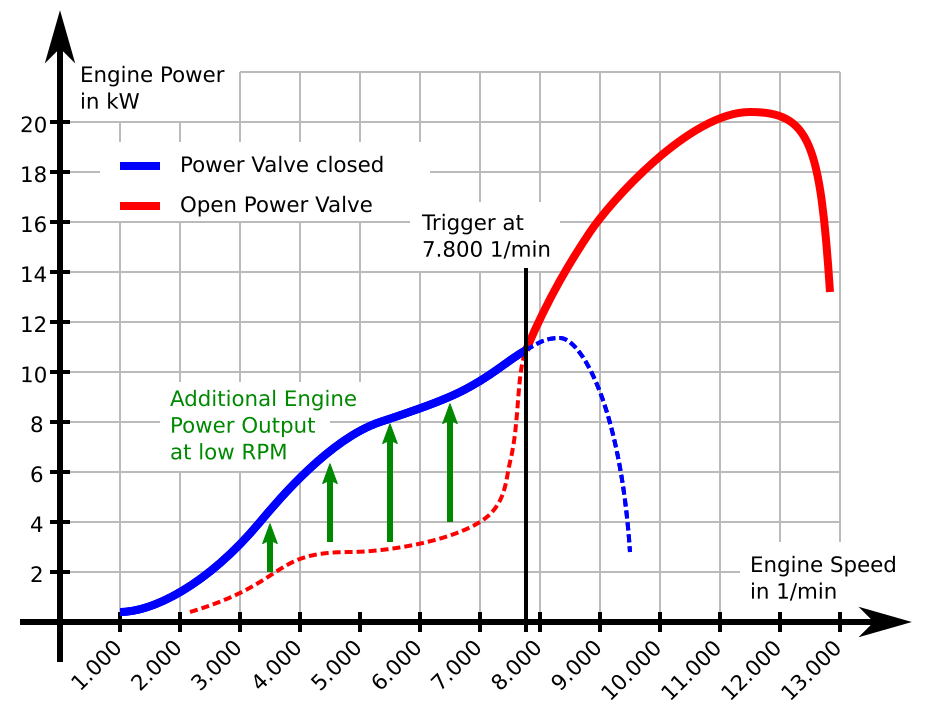
The red curve describes the actual power curve of the engine. Only at about 7,500 rpm the resonance exhaust starts to work, below that the power output is practically non-existent. The blue curve shows the power of the engine with closed power valve.
If you close or open the power valve at the right time, you can switch the engine power characteristics between the two curves shown in the diagram – that’s exactly what the power valve does.
Now you can already see two common problems with this:
- If the engine suddenly starts to pull strongly at 7,500 rpm and the power increases abruptly, the power valve is stuck open and does not close. In most cases it gets stuck because of dirt and combustion residues.
- If the engine does not rotate more than 9,000 rpm, it is possible that the power valve does not open. This may be due to electrical reasons (control unit broken, magnet broken) or mechanical reasons (bowden cable jammed, slider jammed) – in most cases the slider is stuck due to dirt, as already mentioned.
It is also evident that there can be no intermediate positions. The RS250 has two sliders on top of each other to switch between three curves.
The power valve consists of the following components:
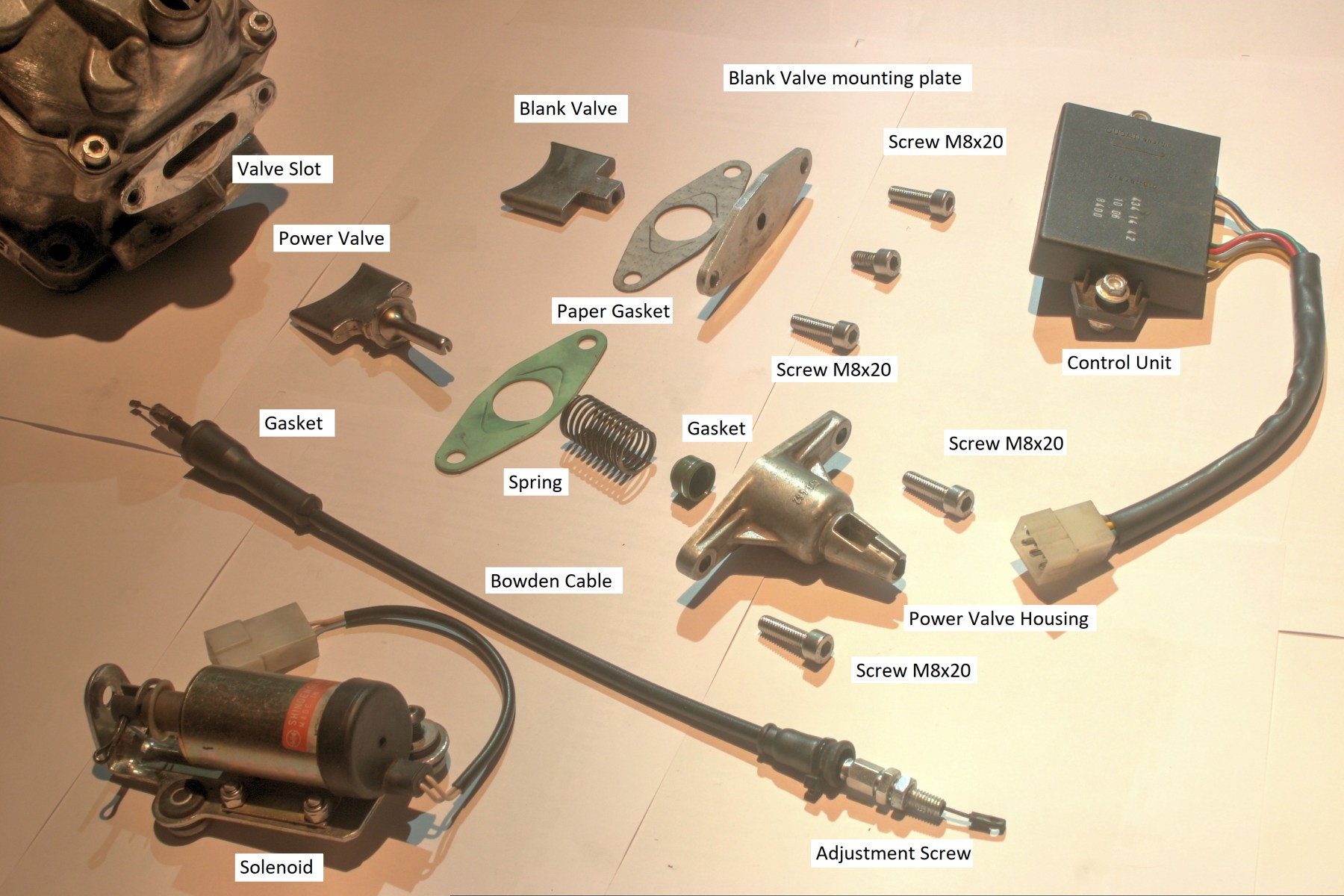
The power valve is therefore put next to the pistons in low speed ranges in order to shorten the control time of the exhaust channel. The control is done electrically depending on the engine speed. This means that the process of compression and the end of flushing starts earlier. This leads to an increase in power at low speeds. Surely the valve, which does not touch the piston, does not seal perfectly, so that one cannot actually speak of changed control times immediately, but the effect is sufficient.
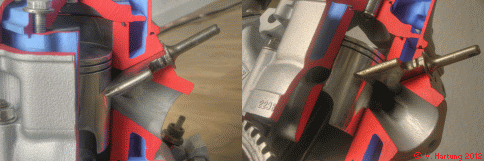